Với những đóng góp không nhỏ, anh đã được Tổng Liên đoàn Lao động Việt Nam trao tặng Giải thưởng Nguyễn Đức Cảnh và Bằng lao động sáng tạo. Người kỹ sư say mê sáng tạo này được đồng nghiệp, bạn bè gọi với cái tên trìu mến: Kỹ sư tiết kiệm điện.
Sáng tạo từ thực tiễn
Nhờ say mê nghiên cứu, cải tiến nên năm nào KS Phăn Văn Hồng cũng đưa ra những giải pháp cải tiến kỹ thuật và được ứng dụng trong hoạt động sản xuất tại đơn vị. Năm 2011, anh nghiên cứu thành công đề tài “Sử dụng bộ điều khiển lập trình PLC S7-200 kết hợp với rơ le dòng điện tự động bù cấp điện áp 6 kV”. Công trình nghiên cứu sáng tạo đã được ứng dụng và làm lợi cho công ty mỗi năm trên 640 triệu đồng, chủ yếu từ việc tiết kiệm điện trong quá trình vận hành của hệ thống.
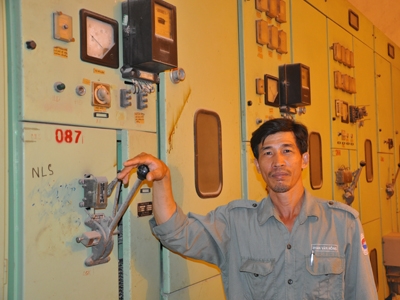 |
KS Phan Văn Hồng tại Trạm phân phối điện của nhà máy sản xuất xi măng Hà Tiên Kiên Giang. |
KS Hồng giải thích: Thiết bị dây chuyền công nghệ sản xuất xi măng của công ty do Trung Quốc thiết kế lắp đặt, trong đó có những thiết bị công suất lớn, sử dụng điện trung thế 6 kV như động cơ nghiền nguyên liệu sống, nghiền xi măng I, II, III.
Nhà thiết kế sử dụng giải pháp bù cos¢ phi cho lưới điện bằng hình thức thủ công, nên khi vận hành công nhân trạm điện phải thường xuyên theo dõi sao cho khi có động cơ máy nghiền hoạt động thì đóng tụ bù phù hợp vào lưới điện, khi máy nghiền ngưng hoạt động thì cắt tụ bù ra khỏi lưới điện.
Với quy trình vận hành như thế, công nhân vận hành trạm điện hết sức vất vả và bị động mà hiệu quả lại không cao. Khi máy nghiền vẫn chạy mà không đóng tụ bù thì công ty phải trả nhiều tiền điện do hiệu suất của thiết bị giảm.
Ngược lại khi máy nghiền dừng mà không ngắt tụ bù khỏi lưới điện thì tốn hao điện, và tụ bù hoạt động một cách vô ích. “Kiểu thiết kế, vận hành bất hợp lý này hao tổn rất nhiều điện, lại không hiệu quả nên tôi quyết tìm cách để vượt qua”- anh Hồng chia sẻ.
Nhằm khắc phục tình trạng nêu trên, anh Hồng đề ra giải pháp như sau: Giữ nguyên thiết bị đang có như tủ điện, tụ bù, đồng hồ hiển thị, rơ le bảo vệ và cảnh báo. Cho vận hành máy nghiền kiểm tra thông số cos¢ của lưới điện khi có đóng tụ bù và không đóng tụ bù. Tính toán lượng dung khán cần thiết bù cho một máy nghiền để cos¢ tương đối đạt từ 0.85 đến 0,98. Dùng rơ le dòng điện samwha eocr giám sát dòng điện động lực trên từng động cơ máy nghiền.
Dùng bộ điều khiển lập trình PLC S7-200 CPU224 nhận tín hiệu dòng điện của từng rơ le dòng điện đưa về. Viết chương trình phần mềm điều khiển hệ thống sao cho khi có máy nghiền nào chạy thì tự động đóng tụ bù phù hợp vào lưới điện nhằm nâng cao hệ số cos¢ tối ưu hiệu suất của thiết bị. Khi máy nghiền nào ngưng hoạt động thì tự động ngắt tụ bù của động cơ máy nghiền đó khỏi lưới điện nhằm tránh lãng phí điện năng cung cấp cho tụ bù. Giải pháp sáng tạo này giúp tiết kiệm 641.981 kWh điện mỗi năm, tương đương gần 642 triệu đồng.
Vượt qua nỗi ám ảnh… tiền điện
Để thành công như ngày hôm nay, người kỹ sư này đã trải qua không ít khó khăn, thậm chí thất bại. Anh Hồng tâm sự: “Đã có những thất bại trong những thử nghiệm ban đầu, phải mày mò làm đi làm lại và cuối cùng thì cũng vượt qua”. Anh cho biết, sự ủng hộ của lãnh đạo và đồng nghiệp là động lực lớn và là điều kiện quan trọng cho sự sáng tạo thành công. “Tôi được sự ủng hộ lãnh đạo cơ quan, anh em đồng nghiệp. Khi tôi có ý tưởng sáng tạo nào đó, có giải pháp trình bày, thường thì Ban Giám đốc đồng ý ngay. Sự phản biện có chăng đó là trao đổi hợp tác”- anh Hồng chia sẻ.
Nói về KS.Hồng, Phó Giám đốc Cty Cổ phần Xi măng Hà Tiên Kiên Giang - ông Nguyễn Thoại Oanh nói: “Anh ấy là một điển hình sáng tạo thông qua thực tiễn. Từ một công nhân siêng năng làm việc, có óc cầu tiến, sau khi học đại học về đã có nhiều sáng kiến cải tiến làm lợi cho Công ty, trong đó có sáng kiến tiết kiệm điện”. Cũng theo Phó giám đốc Oanh, bình quân mỗi năm, nhà máy phải trả khoảng 14 tỷ đồng tiền điện, chiếm 5% giá thành sản phẩm.
Nếu tính tổng các chi phí gồm quản lý, vận chuyển, tiếp thị… thì tiền điện chiếm 10%, tương đương khoảng 28 tỷ đồng. Con số này cho thấy chi phí cho điện luôn là nỗi ám ảnh ảnh hưởng đến lợi nhuận của doanh nghiệp, vì vậy đòi hỏi phải có sự sáng tạo, cải tiến; phải tìm mọi giải pháp để tiết kiệm điện tối đa.
Ông Oanh cho biết, vừa qua có một đoàn của Trung tâm Năng lượng TP.HCM đến khảo sát nhằm giúp cải tiến dây chuyền để tiết kiệm điện, nhưng khi tiếp cận nhà máy của chúng tôi, họ thấy hoàn thiện quá rồi nên đành ra về. Ông Oanh cũng tiết lộ, nhiều doanh nghiệp sản xuất xi măng cũng đang mong muốn học hỏi mô hình này.
Là người đã trực tiếp đến nhà máy xi măng Hà Tiên Kiên Giang, gặp KS. Hồng và xem các sáng kiến của anh, Ông Trương Khắc Thế - Thường trực thi đua của Cty Điện lực Kiên Giang không giấu được cảm xúc. “Đó là một cá nhân điển hình với thành tích nổi bật, có những sáng tạo đột phá, vượt qua khuôn khổ của một nhà máy. Những sáng tạo đó cần được ứng dụng rộng rãi”- ông Thế nói.
Mặc dù có những đóng góp không nhỏ đối với Công ty nói riêng và xã hội nói chung, nhưng người kỹ sư giàu nhiệt huyết sáng tạo này vẫn tự nhìn nhận: “Chưa xứng đáng với lương cơ quan và cơm vợ nuôi ăn học”. Anh vẫn luôn trăn trở với dòng điện, với những bất hợp lý của máy móc và cả những điều vô lý trong kinh doanh và cuộc sống.
KS Phan Văn Hồng đã thành công với đề tài:
-
Cải tiến thiết bị điều chỉnh tốc độ động cơ điện 3 pha dạng VS sang dạng SCR - Năm 2008.
-
Cải tiến cân đóng bao xi măng thành phẩm bằng bộ hiển thị FS 8000A, kết hợp điều khiển lập trình PLC S7-200 - Năm 2009.
-
Sử dụng bộ điều khiển lập trình PLC S7-200 kết hợp với cảm biến, tự động điều khiển công đoạn cấp xi măng cho hệ thống đóng bao - Năm 2010.
-
Sử dụng bộ điều khiển lập trình PLC S7-200 kết hợp với rơ le dòng điện tự động bù cấp điện áp 6 kV - Năm 2011.
-
Cải tiến hệ thống lọc khói bụi lò nung theo nhiệt độ vận hành - Năm 2012.
|