Ứng dụng đèn LED
Hệ thống chiếu sáng ở NMLD Dung Quất với mức tiêu thụ điện trung bình rất lớn, khoảng 12 MWh mỗi ngày (khoảng 4.380 MWh mỗi năm), tính ra tiền điện thắp sáng toàn nhà máy khoảng 13 tỷ đồng/năm. Vì vậy, thực hiện tốt công tác tiết kiệm năng lượng điện chiếu sáng sẽ đem lại hiệu quả lớn.
Hiện nay, với xu hướng phát triển công nghệ xanh và sạch, việc tìm ra và nghiên cứu các ứng dụng thiết thực để đưa vào sử dụng là điều cần thiết. Công nghệ chiếu sáng bằng đèn LED hiệu suất cao cũng không nằm ngoài mục tiêu đó.
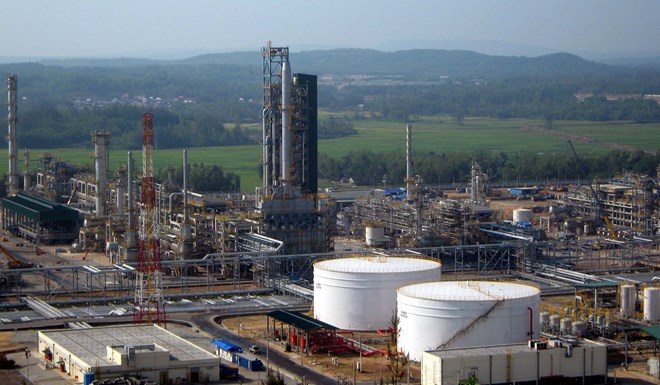
Những sáng kiến của cán bộ, công nhân viên đã giúp Nhà máy vận hành ổn định và tiết kiệm năng lượng - Ảnh:baodautu.vn
|
Theo anh Lê Minh Thuộc, bộ phận bảo dưỡng điện, Phòng Bảo dưỡng sửa chữa BSR cho biết: Đèn LED tiết kiệm được từ 50-80% điện năng so với các loại đèn truyền thống. Tuổi thọ đèn LED có thể kéo dài từ 30.000 giờ đến 50.000 giờ, cao hơn rất nhiều so với các đèn thông thường.
Trong khi đó, đèn sợi đốt tuổi thọ 1.000 giờ, đèn huỳnh quang Compact 10.000 giờ, đèn tuýp huỳnh quang 15.000 giờ, đèn hơi natri cao áp 24.000 giờ. Về mặt môi trường, đèn LED không chứa thủy ngân và hóa chất độc hại, không phát ra tia tử ngoại, thân thiện với môi trường; không tốn chi phí để xử lý rác thải độc hại như các loại đèn huỳnh quang. Thời gian cháy sáng nhanh từ lúc bắt đầu cấp nguồn đến lúc ánh sáng hoàn toàn (ưu điểm so với đèn natri cao áp), không có hiện tượng nhấp nháy, chập chờn.
Sau một năm, tổng số tiền tiết kiệm được trong việc sử dụng đèn tuýp LED tại NMLD Dung Quất là gần 900 triệu đồng. Nếu tính trong 25.000 giờ (hết tuổi thọ của đèn tuýp LED) thì số tiền tiết kiệm được là khoảng là hơn 2,5 tỷ đồng. Môi trường sẽ được hưởng lợi từ việc giảm lượng khí CO2 thải ra cho mỗi kW. Mỗi MWh điện tiết kiệm được sẽ giảm lượng khí thải CO2 bằng 1 tấn.
Tiết kiệm năng lượng từ… hơi
Tại Công ty BSR, có một chương trình mang tên “Tiết kiệm năng lượng và nâng cao độ tin cậy cho hệ thống đường ống condensate trong NMLD Dung Quất”, do kỹ sư Đinh Quang Tứ và cộng sự triển khai.
Anh Tứ cho biết, steam trap (bẫy hơi) là loại thiết bị có chức năng không cho hơi nước (steam) đi qua và chỉ cho nước ngưng (condensate) đi qua sau khi thực hiện trao đổi nhiệt cho các thiết bị và đường ống như heat exchanger (thiết bị trao đổi nhiệt), steam tracing (cuộn ống hơi nước dùng để gia nhiệt cho thiết bị hoặc đường ống)... Theo tính toán của Phòng Điều độ sản xuất BSR, chi phí năng lượng cho trao đổi nhiệt thiết bị công nghệ không bao gồm chi phí cho nhà máy phát điện là khoảng trên 80 triệu USD/năm.
Qua nghiên cứu thực tế các nhà máy sử dụng hơi nước như các nhà máy lọc hóa dầu, nhà máy hóa chất và nhà máy điện trong nước và trên thế giới cho thấy, việc quản lý hệ thống bẫy hơi một cách hiệu quả và tiết kiệm năng lượng là một vấn đề rất khó khăn vì bẫy hơi là thiết bị rất dễ hư hỏng và khó quản lý. Hiện tại tất cả các nhà máy được tìm hiểu trong và ngoài ngành dầu khí chưa có một hệ thống quản lý và đánh giá hệ thống bẫy hơi một cách bài bản.
BSR có số lượng bẫy hơi khoảng 3.720 các loại, việc triển khai hiện đại hóa, tối ưu hóa công tác kiểm tra và sửa chữa bẫy hơi là một thách thức rất lớn. Do đó, việc thiết lập một hệ thống quản lý bẫy hơi hiện đại, không những có ý nghĩa rất lớn về mặt kinh tế năng lượng, mà còn có ý nghĩa nâng cao độ tin cậy vận hành của hệ thống đường ống và toàn nhà máy. Vì sự rò rỉ hơi nước dẫn đến bào mòn hệ thống đường ống rất nhanh chóng.
Đứng trước thực trạng trên, nhóm kỹ sư đưa ra một nhóm giải pháp bao gồm: giải pháp quản lý (khảo sát tại hiện trường, lập danh mục các bẫy hơi, gắn nhãn, lập sơ đồ quản lý các bẫy hơi, thu thập hoàn thiện cơ sở dữ liệu, quản lý tình trạng các bẫy hơi, tính toán lượng hơi thất thoát, lập kế hoạch chuẩn bị vật tư, nhân lực để kiểm tra, sửa chữa); giải pháp kỹ thuật (áp dụng công nghệ, thiết bị dụng cụ chuyên dụng hiện đại Doctor Trap để đo đạc, phân tích, xuất nhanh báo cáo tình trạng của các bẫy hơi đang hoạt động để đưa ra kết luận đúng đắn cho công việc sửa chữa, thay thế).
Quá trình kiểm tra, đo đạc diễn ra khá trơn tru. Theo tính toán, lượng hơi trước khi áp dụng kiểm soát thất thoát 62.620 tấn/năm, với giá khoảng 50 - 55 USD/tấn thì công ty đã giảm thất thoát 3,19 triệu USD/năm. Lợi nhuận thu được sau năm thứ nhất áp dụng là hơn 3 triệu USD. Ngoài ra, lợi ích không đếm được là giảm hư hỏng cho hệ thống đường ống condensate.