PV: Với tiến độ 4 tháng đưa vào vận hành 1 tổ máy, ông đánh giá LILAMA có vai trò quan trọng như thế nào trong thành công của TĐSL?
Ông Nguyễn Thế Trinh: “Tiến độ, chất lượng” luôn là khẩu hiệu nằm lòng của tất cả mọi người, mọi nơi, mọi lúc. Đây là công trình có ý nghĩa quan trọng đặc biệt cả về kinh tế, chính trị, xã hội, nên không thể để xảy ra một sai sót dù nhỏ. Không riêng LILAMA mà tất cả các đơn vị tham gia công trình đều tập trung cao nhất mọi nguồn lực, tài chính, trí tuệ. Với những quyết định chuẩn xác trong cơ chế quản lý của Chính phủ thực hiện dự án theo hướng vừa thiết kế vừa thi công, tiết kiệm thời gian hoặc sử dụng công nghệ bê tông đầm lăn trong thi công để đẩy nhanh tiến độ, chúng tôi có thể tự hào nói rằng, công tác lắp đặt thiết bị 6 tổ máy là một trong những công việc quan trọng nhất, quyết định tiến độ của Thủy điện Sơn La.
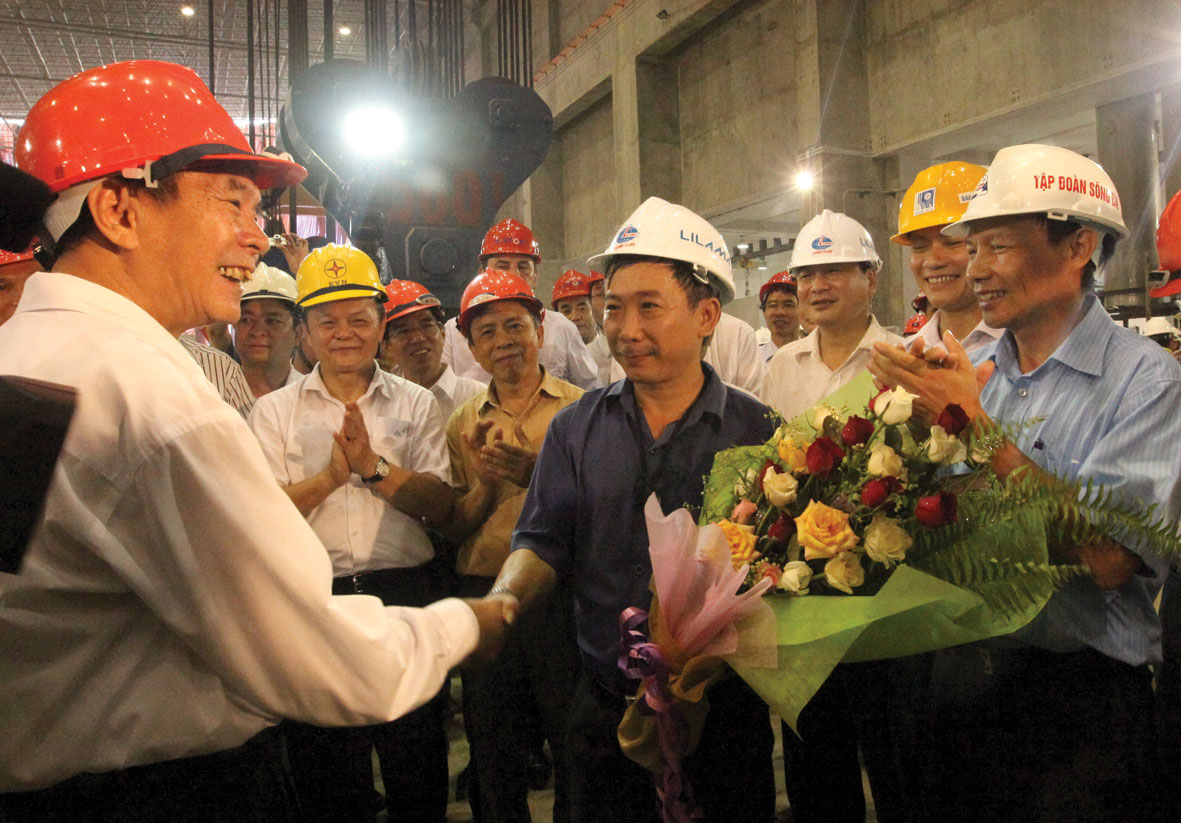
Niềm vui của những người thợ LILAMA khi tổ máy số 6 hòa lưới điện quốc gia - Ảnh Hà Bắc
|
Với tổ máy 1, công việc khá vất vả, vì đây là lần đầu tiên LILAMA lắp đặt những thiết bị “khủng” như thế. Mỗi stator máy phát được chế tạo từ 258.000 tấm tôn silic, mỗi tấm nặng hơn 1 kg, dày 0,5 mm. Với tổ máy đầu tiên, do chưa có kinh nghiệm, chúng tôi phải bố trí khoảng 150 cán bộ, công nhân tỉ mẩn lắp đặt trong vòng 8 tháng. Những tổ máy sau này, do có kinh nghiệm hơn, nên thời gian lắp đặt rút xuống rất nhiều. Phần rotor đường kính 15,586 m được chế tạo từ các tấm tôn dày 5 mm, nặng hơn 35 kg trong điều kiện phải đảm bảo độ tròn với dung sai cho phép. Khó nhất là việc lắp đặt đường ống áp lực nối với buồng xoắn ở độ dốc cao, mỗi ống dài 2 m, đường kính 10,5 m, nặng gần 30 tấn. Việc thi công phải chính xác đến từng chi tiết, đảm bảo đồng tâm, đồng trục, sau đó phải chụp phim, siêu âm các mối hàn 100% không có khuyết tật. Việc lắp đặt từng chi tiết phải đồng bộ với việc đổ bê tông và chuẩn bị mặt bằng. Nếu không đồng bộ thì mọi cố gắng đều đổ xuống sông, xuống biển.
Để đảm bảo tiến độ lắp đặt 4 tháng/tổ máy, ngoài việc cung cấp thiết bị kịp thời của đối tác, tuân thủ kỷ luật lao động, sự tự giác của CBCNV, còn có sự đóng góp quan trọng của hàng trăm sáng kiến, cải tiến kĩ thuật trong thiết kế và thi công. Đó là những sáng kiến ra đời ngay trên công trường thi công và được ứng dụng tại chỗ, có giá trị kinh tế rất cao, làm giảm thời gian thi công, giảm chi phí lắp đặt.
PV: Được biết, đã có khá nhiều sáng kiến bất chợt nảy sinh tại công trường, ông có thể kể lại một vài trong những giây phút “xuất thần” ấy không?
Ông Nguyễn Thế Trinh: Đúng thế, mỗi công trình thủy điện đều có đặc thù về quy mô, điều kiện làm việc, đặc điểm địa chất khí hậu… Vì vậy, rất khó đem kinh nghiệm từ nơi này áp dụng vào nơi khác. Những sáng kiến chỉ có thể nảy sinh trong từng trường hợp cụ thể, từng con người cụ thể, thậm chí có thể chỉ dùng 1 lần, nhưng giá trị vẫn còn mãi mãi.
Ví dụ: Khi thi công lắp van cung xả sâu, theo hướng dẫn của nhà chế tạo thì phải lắp ổ xoay van cung trước, sau đó lắp càng rồi mới lắp thân van cung. Tuy nhiên, khi nghiên cứu tại hiện trường, tôi nhận thấy nếu làm như vậy thì tới khi lắp thân van, bên xây dựng sẽ phải dừng toàn bộ phần đổ bê tông để bên cơ khí thi công và mất rất nhiều thời gian chờ đợi. Tôi đã đề nghị làm ngược quy trình, nghĩa là lắp thân trước, lắp đến đâu đổ bê tông đến đấy, sau đó mới lắp càng rồi lắp ổ. Sáng kiến này có lợi về mặt thời gian lắp máy khoảng 1 tháng, lợi cho đổ bê tông tới 4-5 tháng.
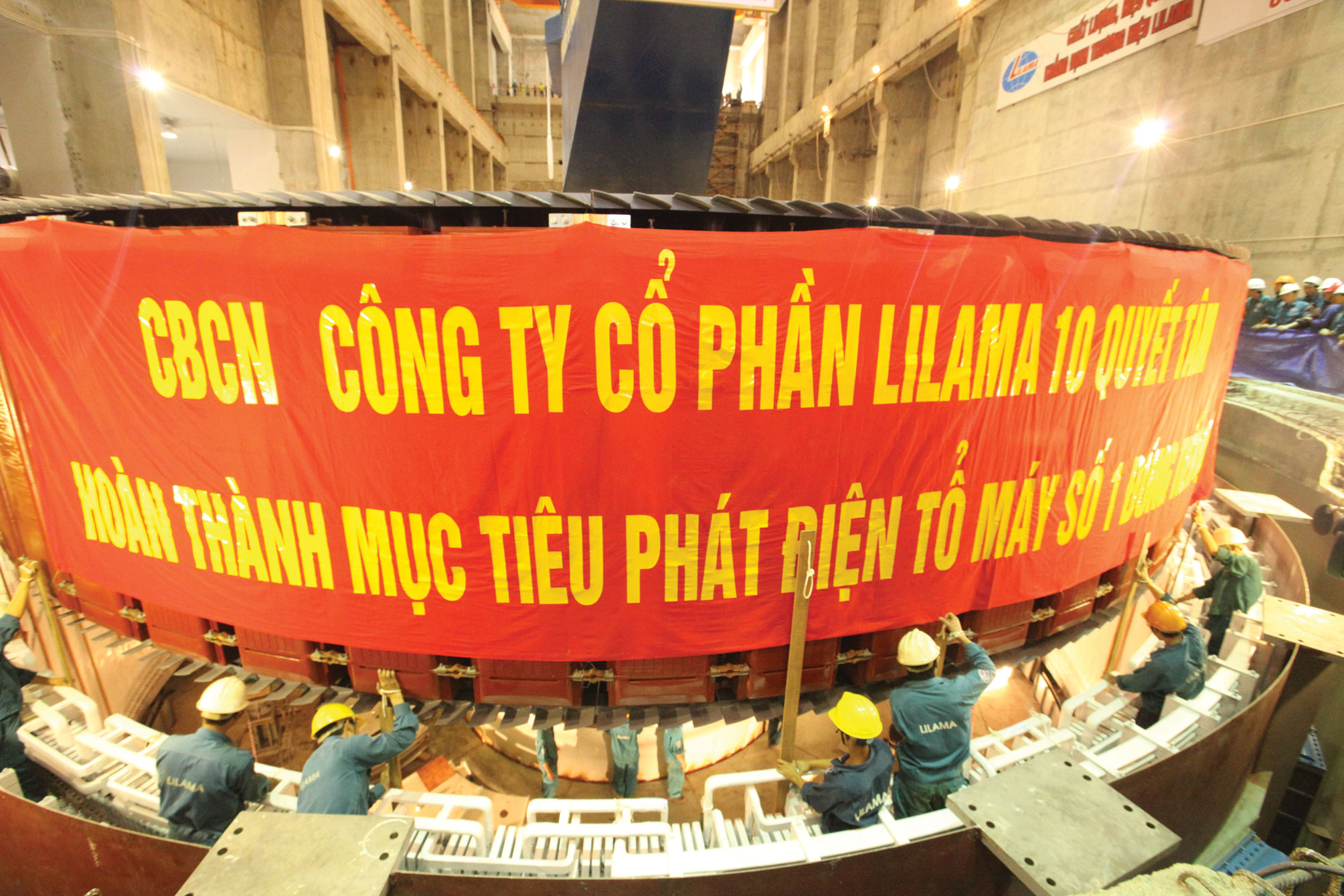
LILAMA luôn đảm bảo tiến độ lắp ráp các tổ máy đúng hẹn - Ảnh Hà Bắc
|
Thứ hai là sáng kiến tổ hợp buồng xoắn và ống khuỷu tại bãi lắp ráp. Theo thiết kế, các thiết bị phải đưa vào tổ hợp tại công trường. Tuy nhiên, đây là những mối hàn gia nhiệt, hàn xong phải có thời gian chờ để ủ nhiệt, sau đó kiểm tra siêu âm và chụp X quang mối hàn, nếu chờ đến khi đưa vào công trường mới lắp ráp thì mất khá nhiều thời gian, trong khi công nhân có sẵn. Thế là chúng tôi cho dựng buồng xoắn tại bãi, hàn trước 14/23 mối hàn, sau đó vận chuyển bán thành phẩm vào công trường. Việc vận chuyển bán thành phẩm có cồng kềnh hơn một chút, nhưng lại tiết kiệm được khá nhiều thời gian tại vị trí lắp đặt.
Thứ ba là sáng kiến tháo dỡ hơn 1.500 tấn giằng tăng cứng để định hình đường ống trong 6 tuyến đường ống áp lực. Theo thiết kế, phải chờ thi công xong toàn bộ phần bê tông bọc đường ống mới được tháo giằng chuyển ra ngoài qua cửa nhận nước và giếng tuabin. Tuy nhiên, do các hạng mục thi công đồng bộ, trong khi chúng tôi thi công đường ống thì cửa nhận nước cũng đã được thử khô và được đóng lại để tích nước. Chúng tôi chỉ còn cách duy nhất là chuyển những thanh giằng ra lối giếng tuabin. Khó là ở chỗ, phải mất khoảng 3 tháng mới tháo xong giằng, nếu cứ chờ đưa giằng ra xong mới lắp tua bin thì không đảm bảo tiến độ. Chúng tôi thấy rằng, có thể cải tiến quy trình bằng cách tháo giằng đến đâu đổ bê tông đến đấy, đổ dần dần để đảm bảo an toàn cho đường ống. Phải mất gần 1 tháng thuyết phục, sáng kiến này mới được chấp nhận. Nhờ đó, công việc này đã rút ngắn được khoảng 4 tháng so với kế hoạch.
Và còn nữa, còn hàng trăm sáng kiến khác góp phần đẩy nhanh tiến độ công trình mà không thể kể hết ra đây.
PV: Đó có phải là những câu chuyện ông nhớ nhất?
Ông Nguyễn Thế Trinh: Thực ra, ấn tượng nhất với tôi lại là những sự kiện khiến cho tiến độ thi công bị ảnh hưởng đôi khi chỉ vì những lý do… lãng xẹt. Ví dụ, thời gian đầu, LILAMA chế tạo thép bọc xả sâu của đập tràn đã bị chậm lại mấy tháng vì khâu kiểm định kết luận là thiết bị vật tư không đảm bảo chất lượng. Phải mất khá nhiều thời gian rà soát lại toàn bộ khâu thủ tục lấy mẫu, thí nghiệm để đi đến kết luận cuối cùng là… vật tư thiết bị không có vấn đề gì mà chỉ là nhầm lẫn trong khâu lấy mẫu, thử nghiệm. Chỉ tiếc mấy tháng trời, người phải chờ việc. Cuối cùng, chúng tôi phải tăng cường lực lượng, động viên công nhân làm đêm làm ngày để bù lại thời gian đã mất.
Lần chạy không tải tổ máy 1 cũng thật vất vả. Hơn 300 thợ LILAMA xoay xở mất 1 ngày đêm mà máy cứ rồ lên rồi lại tắt lịm. Thực ra, ngay từ khi kiểm tra thiết bị trước khi lắp ráp, chúng tôi đã nhận thấy một số kích thước ở trục trên máy phát không chuẩn như bản vẽ. Chúng tôi cũng đã dự đoán trước sự cố có thể xảy ra và có công văn đề nghị chủ đầu tư cảnh báo nhà thầu Alstom về vấn đề này. Có lẽ bên đối tác cũng đã thừa nhận những cảnh báo của ta nên có thể họ đã chế tạo sẵn 1 thiết bị mới, ngay khi được thông báo thiết bị trục trặc, họ đã chuyển luôn thiết bị thay thế bằng đường bộ. Các tổ máy sau thì “ngon” hơn nhiều vì cứ “sao y bản chính” của tổ máy 1 thôi.
.jpg)
Thiết bị nâng hạ cửa van hệ thống nâng thủy lực 2 cần của Tổng công ty Cơ điện Xây dựng Nông nghiệp và Thuỷ lợi - Ảnh CTV
|
PV: Điều gì khiến ông tự hào nhất khi tham gia xây dựng công trình Thủy điện Sơn La?
Ông Nguyễn Thế Trinh: Ngoài Thủy điện Sơn La, LILAMA 10 đã tham gia rất nhiều công trình thủy điện như: Hòa Bình, Vĩnh Sơn, Yaly, Sê San 3, Plei Krông, Buôn kuốp, Sê San 4, Tuyên Quang, Bản Chát, Bắc Hà... Thế nhưng, khi mới nhận nhiệm vụ ở Sơn La, nhìn khối lượng công việc quá đồ sộ, tôi cũng thấy choáng vì không hình dung nổi những việc mình phải làm, cũng không dám nghĩ là có thể phát điện tổ máy 1 vào cuối năm 2010. Chúng tôi động viên nhau, cứ làm rồi khắc đi, khắc đến. Thế rồi, cuối cùng công việc cũng được hoàn thành đúng kế hoạch một cách trôi chảy. Có lẽ đây là niềm vui lớn nhất của những người thợ LILAMA.
Tuy nhiên, điều tôi thấy thanh thản nhất là ở Thủy điện Sơn La, LILAMA đã đảm bảo an toàn lao động tuyệt đối, không thiệt hại gì về người. Sau TĐSL, cái tên LILAMA 10 một lần nữa khẳng định uy tín thương hiệu không chỉ trong lĩnh vực lắp máy mà cả trong lĩnh vực chế tạo cơ khí. Trong số 27.000/73.000 tấn thiết bị cơ khí ở TĐSL được chế tạo trong nước, LILAMA 10 đã chế tạo gần 5.000 tấn, bao gồm 1.800 tấn thiết bị xả sâu, 2.500 tấn thiết bị van hạ lưu và nhiều thiết bị thuỷ công khác, trong đó có sản phẩm cổng trục mang thương hiệu LILAMA 10 là KC 50-36 và KC 50-42 với trọng tải nâng 50 tấn, khẩu độ 42 m. Đồng thời, lắp đặt 73 nghìn tấn thiết bị toàn bộ bao gồm: Thiết bị đập tràn, cửa nhận nước, đường ống áp lực, thiết bị hạ lưu, thiết bị cơ điện, tổ máy… LILAMA 10 đã biến điều không thể thành có thể. Đây là “tấm vé” thông hành rất quan trọng để LILAMA 10 có cơ hội hơn trong việc đấu thầu các dự án trong nước và hợp tác với nước ngoài.
PV: Xin cảm ơn ông!
Một số đơn vị tham gia các hạng mục cơ khí chính của Nhà máy
Công ty CP Cơ điện miền Trung và Công ty CP Cơ khí Điện lực
Phối hợp thực hiện hạng mục đường ống áp lực cho công trình Thủy điện Sơn La.
- Hoàn thành thiết kế và thi công hạng mục đường ống áp lực với khối lượng 9.426 tấn thiết bị được đơn vị tư vấn nước ngoài thẩm định đánh giá cao. Với 100% chất lượng sản phẩm đạt yêu cầu kỹ thuật đề ra.
- Thời gian hoàn thành: 14 tháng, vượt so với tiến độ dự kiến là 6 tháng.
- Tiết kiệm hơn 2 tỷ đồng tiền chi phí do tổ chức sản xuất tốt.
Xí nghiệp Cơ khí Quang Trung
Các hạng mục thi công và cung cấp thiết bị cầu trục cho thủy điện Sơn La:
- Chế tạo thành công hộp giảm tốc hành tinh với lượng chỉ bẳng 1/3 hộp giảm tốc thông thường, tạo ra hiệu suất cao hơn lại tiết kiệm năng lượng bởi bánh răng ăn tới 4/5 răng, lực đẩy từ 1 phía được chuyển vào tâm hướng ra 3 phía. Thành công đó giúp Cơ khí Quang Trung sản xuất ra cẩu trục 560 tấn và 1.120 tấn phục vụ cho Thủy điện Sơn La. Chính cầu trục 1.200 tấn (với tỷ lệ nội địa hóa tới 90%) đã nâng roto nặng 1.000 tấn của các tổ máy Thủy điện Sơn La đặt chính xác vào stato.
- Chế tạo thành công cẩu chân què 350 tấn đặt lên bờ đập ở cao trình 162 m để thử khô các cánh van. Từ đó, Hội đồng nghiệm thu cấp nhà nước mới nghiệm thu các cánh van, đảm bảo các yêu cầu kỹ thuật và cho phép tích nước hồ Thủy điện Sơn La. Sáng kiến đặc biệt này đã góp phần rút ngắn thời gian về đích trước 3 năm.
Tổng công ty Cơ điện Xây dựng Nông nghiệp và Thuỷ lợi
- Chế tạo thiết bị nâng hạ cửa van hệ thống nâng thủy lực 2 cần sức nâng 400 tấn có thể lần lượt đóng 4 cửa van cỗng dẫn dòng của Thủy điện Sơn La. Thời gian thiết kế, chế tạo, thử nghiệm và vận chuyển 1468 tấn thiết bị từ Hà Nội đến công trường với thời gian kỷ lục là 28 ngày. Với thiết bị nâng hạ cửa van này không chỉ đảm bảo tiến độ công trình Thuỷ điện Sơn La mà còn giúp giảm chi phí so với việc nhập ngoại.
- Chế tạo thành công hệ thống thiết bị nâng hạ cửa van với hệ thống điện tự động hoá hiện đại, áp dụng những công nghệ mới nhất về cảm biến tải, cảm biến hành trình, mắt thần thuỷ lực, soi lỗ chốt.... với tính năng có thể tháo lắp được, hệ thống thiết bị này sẽ được chuyển đến công trình thuỷ điện khác tương tự như thiết kế của Thủy điện Sơn La, tiết kiệm cho đất nước.
|